[su_panel background=”#555555″ color=”#ffffff” border=”3px solid #66cc99″ shadow=”0px 1px 2px #66cc99″ radius=”20″ target=”blank”]
3D scanning is a relatively new technology.
However, 3D Scanning is useful for guiding the creation of CAD data for obsolete parts and recreating complex 3D geometry. We can take your product, 3D scan it, and then use the scan data for reverse engineering, 3D printing, or even product visualisation and rendering. [/su_panel]
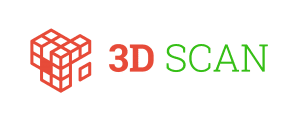
However, 3D Scanning is useful for guiding the creation of CAD data for obsolete parts and recreating complex 3D geometry. We can take your product, 3D scan it, and then use the scan data for reverse engineering, 3D printing, or even product visualisation and rendering. [/su_panel]
Client Benefits
[su_icon_text color=”#ffffff” icon=”icon: check” icon_color=”#66cc99″ icon_size=”40″]Cost-effective 3D Scanning
3D Scans can take between 30 minutes and a few hours, depending on the size and complexity of the part
Convert your product into a 3D digital file with an accuracy of up to 50 microns
3D scan objects from 30mm cubed up to 1200mm cubed in full colour or black and white [/su_icon_text] [su_icon_text color=”#ffffff” icon=”icon: check” icon_color=”#66cc99″ icon_size=”40″]Convert existing parts into 3D data
3D Print
3D content for websites and interactive documents
Full CAD remodel using scan data as a reference
[/su_icon_text] [su_icon_text color=”#ffffff” icon=”icon: check” icon_color=”#66cc99″ icon_size=”40″]3D Scanning Alternatives
Reverse Engineer components without 3D scanning them
CAD models are created by combining physical measurements, engineering expertise, and any drawing data that may be available.
Ideal for small parts where geometry can be determined or measured quicker and easier than using a 3D Scan
CAD data is compatible with all manufacturing processes. [/su_icon_text][su_icon_text color=”#ffffff” icon=”icon: check” icon_color=”#66cc99″ icon_size=”40″]Full In-House service
| 3D CAD | 3D Scan | 3D Print | 2D CAD | Drawings printed up to A1 |
| Design | Analyse | Visualise | Animate |
[/su_icon_text]
3D Scans can take between 30 minutes and a few hours, depending on the size and complexity of the part
Convert your product into a 3D digital file with an accuracy of up to 50 microns
3D scan objects from 30mm cubed up to 1200mm cubed in full colour or black and white [/su_icon_text] [su_icon_text color=”#ffffff” icon=”icon: check” icon_color=”#66cc99″ icon_size=”40″]Convert existing parts into 3D data
3D Print
3D content for websites and interactive documents
Full CAD remodel using scan data as a reference
[/su_icon_text] [su_icon_text color=”#ffffff” icon=”icon: check” icon_color=”#66cc99″ icon_size=”40″]3D Scanning Alternatives
Reverse Engineer components without 3D scanning them
CAD models are created by combining physical measurements, engineering expertise, and any drawing data that may be available.
Ideal for small parts where geometry can be determined or measured quicker and easier than using a 3D Scan
CAD data is compatible with all manufacturing processes. [/su_icon_text]
| 3D CAD | 3D Scan | 3D Print | 2D CAD | Drawings printed up to A1 |
| Design | Analyse | Visualise | Animate |
[/su_icon_text]
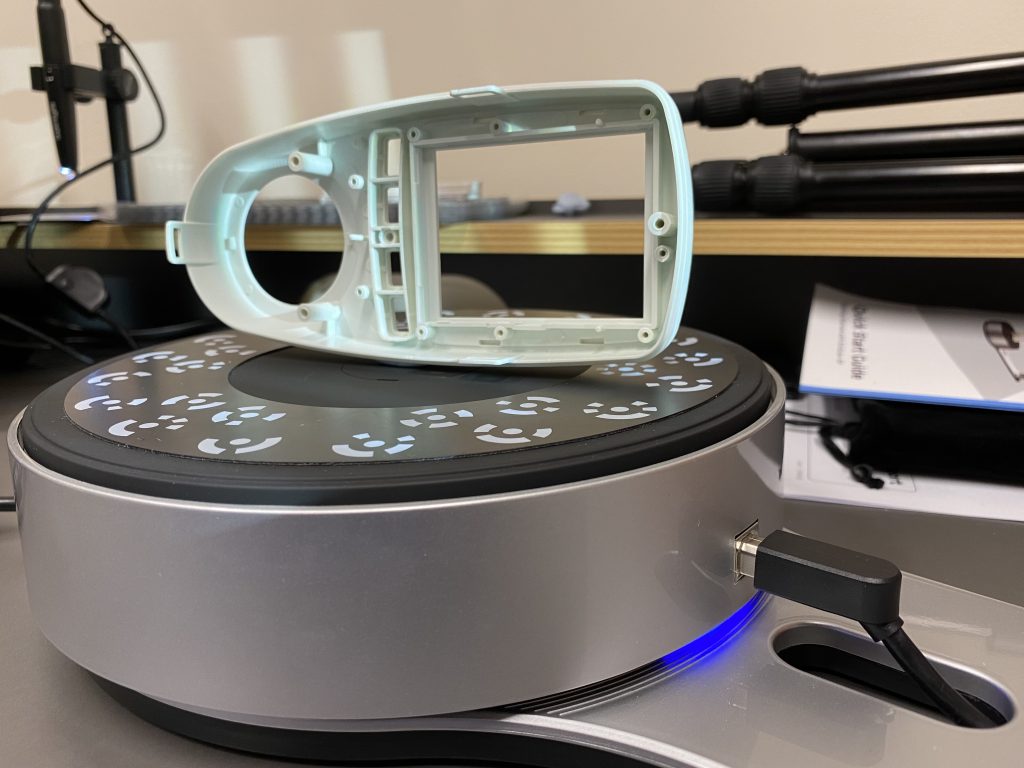
You must be logged in to post a comment.